Понимание тепловых систем ─ Как различные технологии влияют на отверждение порошка
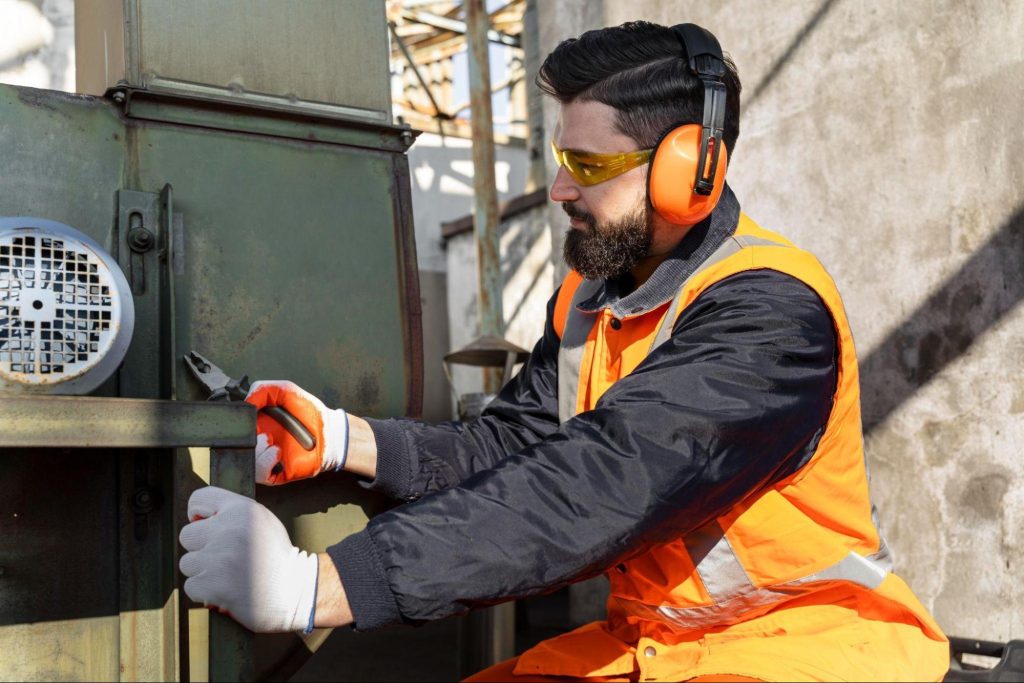
Содержание
В мире производства и отделки процесс отверждения порошковых покрытий является свидетельством современной инженерии и химии. Этот сложный процесс, который превращает порошок в прочное долговечное покрытие, в значительной степени зависит от тепловых систем и их способности равномерно и эффективно распределять тепло.
При более внимательном рассмотрении этих систем мы можем понять нюансы, которые определяют успех или неудачу процесса отверждения порошка.
Механизмы теплопередачи в процессах отверждения порошков
В области отверждения порошка первостепенное значение имеет экспертиза тонкостей механизмов передачи тепла. В среде печи отверждения три основных механизма — проводимость, конвекция и излучение — взаимодействуют синергетически, способствуя процессу отверждения.
Теплопроводность осуществляется посредством прямого прикосновения, передавая тепло от поверхностей печи к отверждаемым деталям.
Конвекция, с другой стороны, основана на циркуляции теплого воздуха внутри печи, охватывающего элементы для обеспечения равномерного нагрева. Между тем, излучение использует электромагнитные волны для передачи тепловой силы порошковому покрытию, дополняя альтернативные механизмы.
Достижение наиболее выгодного равновесия между этими механизмами имеет решающее значение для обеспечения полного плавления, текучести и отверждения порошка, что приводит к идеальной отделке, характеризующейся как эстетической привлекательностью, так и долговечностью. Таким образом, тонкое понимание динамики переключения тепла необходимо для оптимизации тактики отверждения порошка и достижения неизменно отличных эффектов в коммерческих приложениях.
Сравнительный анализ печей для порошковой окраски и промышленных печей
Источник: rohnerspraybooths.com
Если углубиться в оборудование, то печи для порошковой окраски и промышленные печи выполняют схожие, но в то же время различные функции. Хотя обе они предназначены для создания высоких температур, необходимых для отверждения, печи для порошковой окраски специально разработаны для процесса отверждения порошка.
Они часто имеют усовершенствованные конструкции воздушного потока для обеспечения равномерного нагрева и откалиброваны для отверждения порошковых покрытий в точных температурных диапазонах. Промышленные печи, с другой стороны, более универсальны, обслуживая более широкий спектр процессов, включая, но не ограничиваясь отверждением. Отличие заключается в настройке; печи для порошкового покрытия точно настроены для оптимальной эффективности отверждения порошка.
Влияние методов нагрева на эффективность отверждения порошка
Эффективность отверждения порошка во многом зависит от используемой технологии нагрева. Обычные конвекционные печи, долгое время являющиеся опорой предприятия, славятся своими надежными и устойчивыми профилями нагрева. Тем не менее, ландшафт развивается с появлением инфракрасной и ультрафиолетовой технологии отверждения, предоставляя более рационализированные альтернативы.
Эти инновации обеспечивают улучшенные процессы отверждения, немедленно фокусируясь на материале порошкового покрытия, минуя чрезмерный нагрев подложки. Следовательно, они не только обещают более быстрое время отверждения, но и дополнительно обеспечивают значительную экономию электроэнергии и сокращение интервалов цикла.
Соответственно, стратегический выбор метода нагрева становится ключевым аспектом, оказывающим глубокое влияние как на стоимость выпускаемой продукции, так и на обычное энергопотребление в процессе нанесения порошкового покрытия.
Тепловая однородность и ее роль в достижении оптимальных результатов отверждения порошка

Источник: reliantfinishingsystems.com
В мире порошковой вулканизации достижение тепловой однородности в камере печи становится краеугольным камнем для достижения безупречных результатов. Значение этой однородности невозможно переоценить, поскольку даже незначительные несоответствия температуры могут привести к появлению множества дефектов пола, что снижает общее превосходство готового продукта.
Эти дефекты представляют собой целый спектр проблем, начиная от визуально раздражающего эффекта «апельсиновой корки» и заканчивая более обширными дефектами, включая отверстия и изменение цвета.
Для решения этой жизненно важной проблемы решающую роль играют усовершенствованные конструкции печей и точные структуры управления. Сложные архитектуры печей проектируются с тщательным интересом к элементу, используя методы вместе с оптимизированными стилями воздушного потока и стратегиями изоляции для обеспечения равномерного распределения тепла в определенной точке камеры.
Дополнением к этим конструкциям являются современные управляющие структуры, которые работают в тандеме с датчиками, стратегически расположенными в среде печи. Эти структуры постоянно отслеживают изменения температуры и автономно регулируют нагревательные элементы и поток воздуха для поддержания желаемого теплового равновесия на протяжении всего цикла отверждения.
Результатом этих усилий является гарантия того, что каждая деталь, независимо от ее расположения в печи, подвергается равномерной обработке.
Тщательно контролируя однородность нагрева, производители могут соблюдать самые строгие первоклассные требования, снижать риск возникновения дефектов и поставлять продукцию, которая соответствует или превосходит ожидания клиентов.
Эта точность не только усиливает визуальное очарование готового продукта, но и дополнительно укрепляет его механические свойства, способствуя его прочности и производительности в реальных программах. В конечном счете, именно благодаря синергии современных конструкций и точно обработанных структур достигается стремление к безупречным результатам отверждения порошка.
Вопросы потребления энергии в различных системах отопления
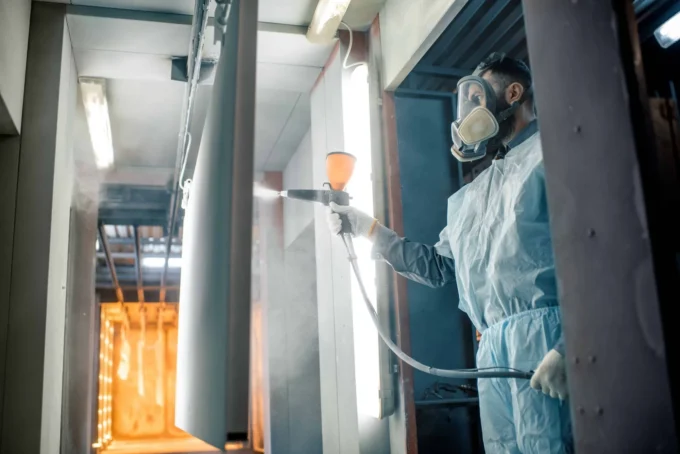
Источник: tiger-coatings.com
Потребление энергии является существенным фактором при оценке тепловых структур для пакетов отверждения порошка. Традиционные конвекционные печи, известные своей эффективностью, часто влекут за собой гигантские расходы на электроэнергию, как правило, из-за необходимости нагревать большие объемы воздуха внутри камеры печи.
Напротив, инфракрасные и УФ-структуры отверждения предоставляют убедительную возможность, характеризующуюся улучшенной энергоэффективностью. Благодаря своей способности концентрировать электричество непосредственно на порошковой ткани вместо рассеивания его в окружающем воздухе, эти системы уменьшают потери и оптимизируют использование энергии.
Эта целенаправленная технология не только ускоряет процедуру отверждения, но и приносит большую пользу окружающей среде, способствуя сокращению выбросов углерода и экономии энергии.
Более того, хотя предварительное финансирование этих передовых технологий может быть выше, их долгосрочная ценовая эффективность станет очевидной за счет снижения эксплуатационных расходов и превосходной устойчивости, что соответствует современным тенденциям в области более экологичных методов производства.
Изучение передовых технологий для улучшения контроля и точности при отверждении порошков
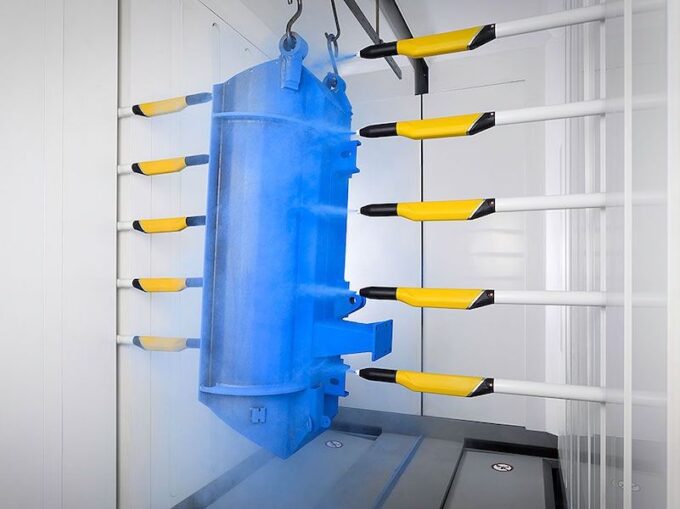
Источник: finishingandcoating.com
В неустанном стремлении к совершенству в процессах отверждения порошков отрасль приняла ряд передовых технологий. Эти инновации представляют собой квантовый скачок в точности и контроле, революционизируя стандарты качества конечного продукта. Умные печи, оснащенные сложными системами мониторинга в реальном времени и адаптивного управления, олицетворяют эту технологическую эволюцию.
Динамически регулируя процесс отверждения в соответствии с уникальными характеристиками каждого покрытия и подложки, эти системы гарантируют непревзойденную точность. Этот скрупулезный подход не только оптимизирует условия отверждения, но и последовательно обеспечивает превосходное качество отделки и исключительную долговечность, устанавливая новые стандарты в этой области.
Эволюция систем нагрева в процессе отверждения порошка является свидетельством неустанного стремления к качеству и эффективности в производстве. Поскольку мы продолжаем расширять границы технологий, обещание еще более эффективных, точных и устойчивых методов отверждения порошка становится все более ощутимым.
С каждым достижением мы не только улучшаем эстетические и функциональные качества изделий с покрытием, но и вносим вклад в более устойчивое и эффективное производство.